As the demand for animal feed continues to grow, feed producers are constantly seeking ways to optimize the efficiency of their production equipment. A 10 t/h animal feed manufacturing machine is a significant investment, and maximizing its output is crucial for maintaining profitability. While these machines are designed to operate efficiently, there are several technical upgrades and improvements that can further enhance their production capabilities. This article explores some of the key areas where technological advancements can boost the efficiency of a 10 t/h animal feed manufacturing machine.
1. Automation and Control Systems
One of the most effective ways to improve the efficiency of a 10 t/h animal feed manufacturing machine is by upgrading its automation and control systems. Implementing advanced programmable logic controllers (PLCs) and human-machine interfaces (HMIs) can provide better control over the production process, leading to increased output and reduced waste.
- Improved Process Control: Advanced control systems can precisely monitor and adjust critical parameters such as feed rate, temperature, and moisture content. This level of control helps maintain consistent product quality and minimizes the risk of production issues.
- Automated Material Handling: Integrating automated material handling systems, such as conveyors and bucket elevators, can streamline the movement of raw materials and finished products through the machine. This reduces manual labor and minimizes the risk of errors or delays in the production process.
- Real-Time Monitoring: Modern control systems often include real-time monitoring capabilities, allowing operators to track key performance indicators (KPIs) such as production output, energy consumption, and equipment utilization. This data can be used to identify areas for improvement and optimize the production process.
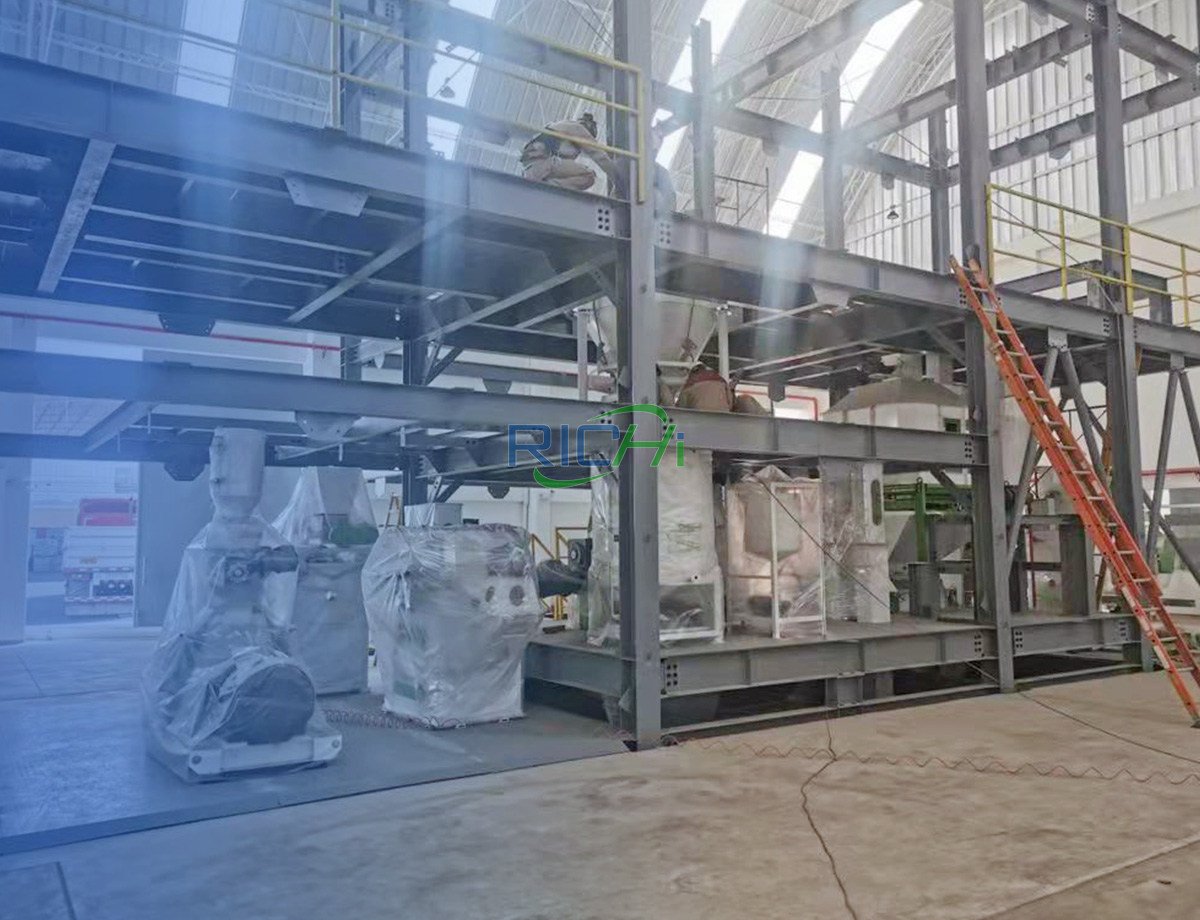
2. Pelleting Technology Upgrades
For machines equipped with pelleting systems, upgrading the pelleting technology can significantly improve efficiency and product quality.
- Die and Roll Upgrades: Replacing worn or outdated dies and rolls with newer, more efficient designs can enhance pellet quality and increase production output. Advanced die and roll materials, such as chrome or tungsten carbide, can also extend their lifespan and reduce maintenance requirements.
- Conditioner Upgrades: Improving the conditioning system, which prepares the feed mixture for pelleting, can enhance the effectiveness of the pelleting process. Upgrades such as increased steam injection or improved mixing can improve pellet quality and reduce energy consumption.
- Pellet Mill Upgrades: Replacing older pellet mill components with more efficient designs can boost production output and reduce maintenance costs. This may include upgrading the gearbox, bearings, or other critical components.
3. Energy-Efficient Components
Upgrading to more energy-efficient components can significantly reduce the operating costs of a 10 t/h animal feed making machine, contributing to improved overall efficiency.
- High-Efficiency Motors: Replacing standard electric motors with premium efficiency or IE3 class motors can reduce energy consumption by up to 3-5% . This upgrade can lead to substantial cost savings over the machine’s lifetime.
- Variable Frequency Drives (VFDs): Installing VFDs on the machine’s motors allows for better control of speed and torque, optimizing energy usage based on production demands. VFDs can reduce energy consumption by up to 30% compared to direct-on-line starters .
- Heat Recovery Systems: Implementing heat recovery systems can capture excess heat generated during the pelleting process and reuse it for conditioning or other purposes. This not only improves energy efficiency but also reduces overall production costs.
4. Maintenance and Reliability Upgrades
Improving the maintenance and reliability of a 10 t/h animal feed manufacturing machine can minimize downtime, reduce repair costs, and enhance overall efficiency.
- Predictive Maintenance: Upgrading to a predictive maintenance system, which uses sensors and data analysis to predict when components will fail, can help prevent unexpected breakdowns and optimize maintenance schedules. This approach can reduce maintenance costs by up to 30% compared to traditional reactive maintenance .
- Wear Parts Monitoring: Integrating wear parts monitoring systems, which track the condition of critical components such as dies and rolls, can help optimize replacement schedules and minimize the risk of production issues due to worn parts.
- Lubrication System Upgrades: Upgrading the machine’s lubrication system, such as implementing automatic lubrication or using higher-quality lubricants, can extend the lifespan of components and reduce maintenance requirements.
5. Process Optimization
In addition to technical upgrades, optimizing the production process can also improve the efficiency of a 10 t/h animal feed manufacturing machine.
- Raw Material Preparation: Ensuring that raw materials are properly cleaned, sized, and conditioned before entering the machine can enhance the effectiveness of the production process and reduce wear on components.
- Operator Training: Providing comprehensive training to machine operators on proper operation and maintenance procedures can help maximize the machine’s efficiency and minimize the risk of errors or misuse.
- Continuous Improvement: Fostering a culture of continuous improvement, where employees are encouraged to suggest and implement ideas for optimizing the production process, can lead to ongoing efficiency gains over time.
Conclusion
Improving the production efficiency of a 10 t/h animal feed manufacturing machine through technical upgrades and process optimization can lead to significant benefits, including increased output, reduced operating costs, and improved product quality. By investing in upgrades such as automation and control systems, pelleting technology improvements, energy-efficient components, and maintenance reliability enhancements, feed producers can maximize the return on their equipment investment and stay competitive in the market.As the animal feed industry continues to evolve, embracing technological advancements and implementing continuous improvement strategies will be essential for feed producers looking to maintain a leading edge in the production of high-quality animal feed.