Wood chip dryers play a vital role in the wood processing industry, especially in the production of high-quality wood pellets. These machines are designed to reduce the moisture content of wood chips and sawdust, ensuring optimal conditions for further processing. However, optimizing wood chip dryers for different production scales necessitates careful consideration of various factors. This article delves into strategies for optimizing wood chip dryers for small, medium, and large-scale production.
Understanding Wood Chip Dryers
Wood chip dryers typically utilize hot air or steam to evaporate moisture from wood chips, sawdust, and other biomass materials. Common types of wood chip dryers include:
- Rotary Drum Dryers: These dryers feature a rotating drum that tumbles the wood chips while hot air passes through, ensuring even drying.
- Fluidized Bed Dryers: These dryers use hot air to suspend and dry the wood chips, creating a fluid-like motion that enhances heat transfer and drying efficiency.
- Belt Dryers: These dryers employ a conveyor belt to move the wood chips through a heated chamber, providing continuous drying.
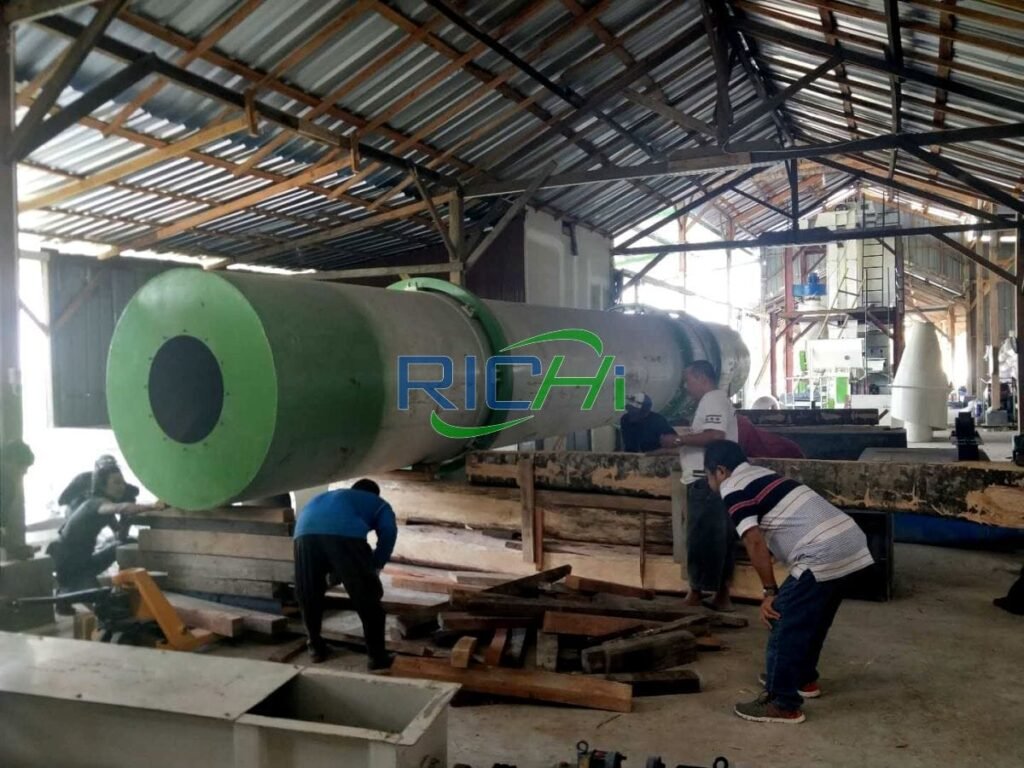
Optimizing for Small-Scale Production
Small-scale production typically involves processing up to a few tons of wood chips or sawdust per hour. Strategies for optimization in this context include:
- Compact Design: Small-scale operations benefit from compact dryer designs that fit within limited spaces. Smaller rotary drum dryers are ideal for such setups.
- Energy Efficiency: Energy costs can significantly impact small-scale operations. Employing dryers with heat recovery systems and energy-efficient motors can help reduce operational expenses.
- Automation: Implementing basic automation features, such as moisture sensors and automated control systems, can enhance drying consistency and lower labor costs.
- Modular Systems: Modular dryer systems facilitate easy expansion as production demands grow. Starting with a smaller unit and adding modules can be a cost-effective strategy.
Example: RICHI Machinery offers compact rotary drum dryers suitable for small-scale operations, designed for high efficiency and customization to fit specific production needs.
Optimizing for Medium-Scale Production
Medium-scale production involves processing several tons of wood chips or sawdust per hour. Optimization strategies for this scale include:
- Balanced Capacity: Selecting a dryer with a capacity that aligns with production volume is crucial. Over-sizing can lead to inefficiencies, while under-sizing can create bottlenecks.
- Advanced Control Systems: Implementing advanced control systems with real-time monitoring and automated adjustments ensures consistent drying and optimal energy use.
- Heat Recovery: Utilizing heat recovery systems to recycle thermal energy from exhaust air can significantly enhance energy efficiency.
- Integrated Solutions: Integrating the dryer with other processing equipment, such as pellet mills and conveyors, can streamline operations and boost overall efficiency.
Example: Vina Nha Trang provides wood chip dryers with capacities ranging from 6,000 to 14,000 kg/h, featuring advanced control systems and heat recovery options that make them suitable for medium-scale production. (Related post: wood chipper price )
Optimizing for Large-Scale Production
Large-scale production involves processing tens of tons of wood chips or sawdust per hour. Strategies for optimizing dryers at this scale include:
- High-Capacity Dryers: Large-scale operations require high-capacity dryers capable of handling substantial volumes. Rotary drum dryers with large drums or multi-pass systems are suitable for such needs.
- Comprehensive Automation: Fully automated systems equipped with advanced sensors, real-time monitoring, and automated adjustments ensure optimal performance and reduced labor costs.
- Energy Management: Implementing sophisticated energy management systems that optimize fuel use and incorporate renewable energy sources can lower operational costs and environmental impact.
- Redundancy and Reliability: Ensuring redundancy in critical components and utilizing robust, reliable equipment minimizes downtime and maintains continuous production.
Example: The ONIX Corporation offers large-scale rotary drum dryers designed for high-capacity operations, featuring comprehensive automation and energy management systems that cater to industrial-scale production.
Key Considerations for Optimization
Regardless of production scale, several key factors are essential for optimizing wood chip dryers:
- Material Characteristics: Understanding the specific characteristics of the wood chips or sawdust being processed is crucial. Factors such as initial moisture content, particle size, and density affect drying efficiency and equipment selection.
- Energy Source: Choosing the right energy source for the dryer can influence both operational costs and environmental footprint. Options include natural gas, biomass, and electricity.
- Maintenance: Regular maintenance is vital for ensuring optimal performance and longevity of the dryer. Establishing a maintenance schedule and training staff on proper maintenance procedures can prevent unexpected downtime.
- Safety: Equipping the dryer with safety features, such as fire detection and suppression systems, is critical to prevent accidents and ensure safe operation.
Case Study: Germany
Germany is known for its stringent environmental regulations and advanced industrial technologies. Optimizing wood chip dryers in Germany involves:
- Energy Efficiency: German manufacturers prioritize energy efficiency, often incorporating heat recovery systems and energy-efficient motors.
- Automation: Advanced automation systems with real-time monitoring and data analytics are standard, ensuring consistent drying and optimal performance.
- Environmental Compliance: Adhering to strict environmental regulations requires robust emission control systems and sustainable energy sources.
Example: Dorset Group offers wood chip dryers that utilize residual heat for drying, enhancing energy efficiency and minimizing environmental impact. Their dryers are designed for continuous operation and feature advanced control systems.
Conclusion
Optimizing wood chip dryers for various production scales requires careful consideration of factors such as capacity, energy efficiency, automation, and integration with other processing equipment. By selecting the right dryer and implementing best practices, businesses can achieve consistent, high-quality drying of wood chips and sawdust, leading to superior end products and improved operational efficiency.
Companies like RICHI Machinery, Vina Nha Trang, and The ONIX Corporation provide a range of wood chip dryers suitable for different production scales, each with unique features and capabilities. By leveraging the expertise of these manufacturers and tailoring solutions to specific needs, businesses can optimize their wood chip drying processes and achieve long-term success in the wood processing industry.
For details please contact: Richi Pellet Machine
WhatsApp:86 138 3838 9622
Email:enquiry@richipelletmachine.com