The technical advantages achieved by RICHI’s efforts in floating fish feed making machines over the years are fully reflected in the floating fish feed production line.
Simple operation, easy to learn, precise parameter control, to ensure that the product is completed in a specific temperature, pressure, humidity and time.
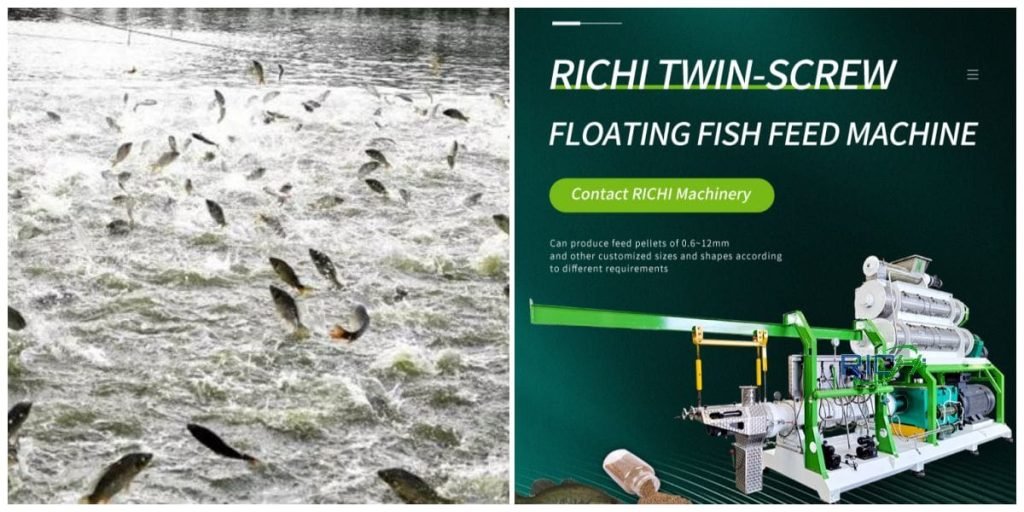
Reasonable structure design, special material, fast self-cleaning performance to ensure mechanical stability and easy maintenance, colorful shapes and flavors to meet the requirements of various fish pet food.
Related post: Floating Fish Feed Mill
When choosing aquafeed floating fish feed production line, you must first understand the many characteristics of aquafeed:
(1)Small pellet size. Due to the short digestive tract of aquatic animals and related physiological characteristics, in order to speed up digestion and absorption, the crushed pellet size of aquatic feed should be smaller than that of livestock and poultry feed.
For example, in the production of eel and shrimp feed, the pellet size should reach 80 mesh to 120 mesh.
(2)High protein content and low carbohydrate content. The protein content of livestock and poultry feeds is generally less than 20%, while the protein content of aquatic animal feeds is mostly 30% to 40%, and the protein content of turtle and eel feeds is as high as 65% to 70%.
(3)The pellet feed has a compact structure, high cohesion and water resistance, and the stability of the pellet feed in water for more than 2 hours is required for fish feed.
(4)In the production of aquatic feed, cross-contamination is strictly prohibited. Some raw materials need to be treated aseptically.
The selected floating fish feed making machine is easy to clean and has less residue. Especially in the production of floating feed, shrimp and eel feed, other types of feed should not be produced at the same time to prevent cross-production pollution.
To produce high-quality aquatic feed, we must rely on scientific and reasonable processing technology and combine it with advanced, reliable and stable floating fish feed making machine. In this regard, the choice of floating fish feed making machine is particularly critical.
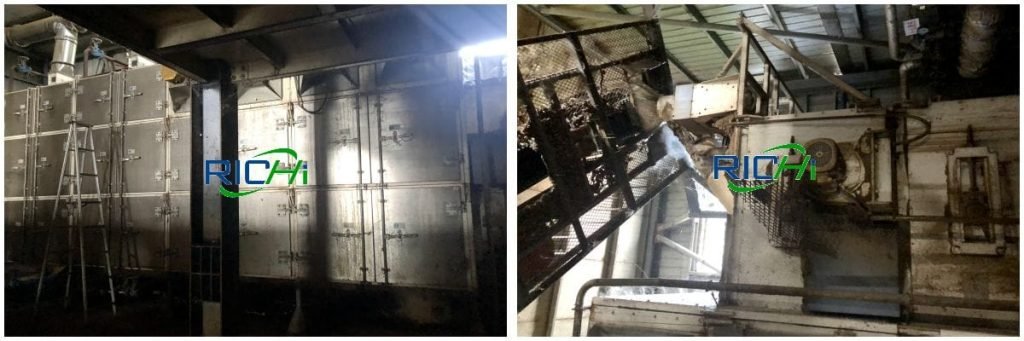
Related post: 3-4T/H Floating Fish Feed Production Line
1. Process flow of fish feed production line:
The floating fish feed making machine production line can process pellet feeds such as pigs, cattle, sheep, rabbits, chickens, ducks, fish, etc. The traditional processing method is several times more efficient, and it is suitable for large-scale farms and floating fish feed mills to produce full-price feed and the transformation of pellet feed plants.
It can also produce saw wood pellets, wood powder pellets and straw pellets, etc. It is a pellet processing unit with a high degree of automation. It is a floating fish feed making machine that uses corn, soybean meal, wheat, sorghum, straw, grass, rice husk, etc. as raw materials, crushes the raw materials, and directly presses them into pellets.

2. Features of fish feed pellet machine production line:
- This series of floating fish feed making machines adopt a steam conditioner, so that the material can be fully matured and the quality of the pellets can be ensured.
- The main drive adopts high-precision gear drive, and the output is about 20% higher than that of the belt drive type.
- Imported high-quality bearings and oil seals are selected to ensure stable operation, low noise and high efficiency of the whole machine.
- The feeder adopts frequency conversion motor to ensure the quality of pellet discharge.
- A variety of aperture ring dies are available for selection. The floating fish feed making machine ring dies have long service life, smooth granulation and high quality.
- Compensation type serpentine spring coupling of international advanced level, with novel structure, compactness, safety, low noise and low failure performance.
3.Floating fish feed machine production line process
Floating fish feed making machine is usually selected according to the production scale, production varieties, and production process conditions. Therefore, different floating fish feed mills often use different equipment. However, some basic floating fish feed making machine for feed processing is the same.
According to the floating fish feed making machine line process flow, it generally includes raw material receiving and cleaning equipment, conveying equipment, crushing equipment, batching equipment, mixing equipment, floating pellet machine, floating fish feed extruder machine, liquid spraying equipment, ventilation and dust removal equipment, packaging equipment and central control system.
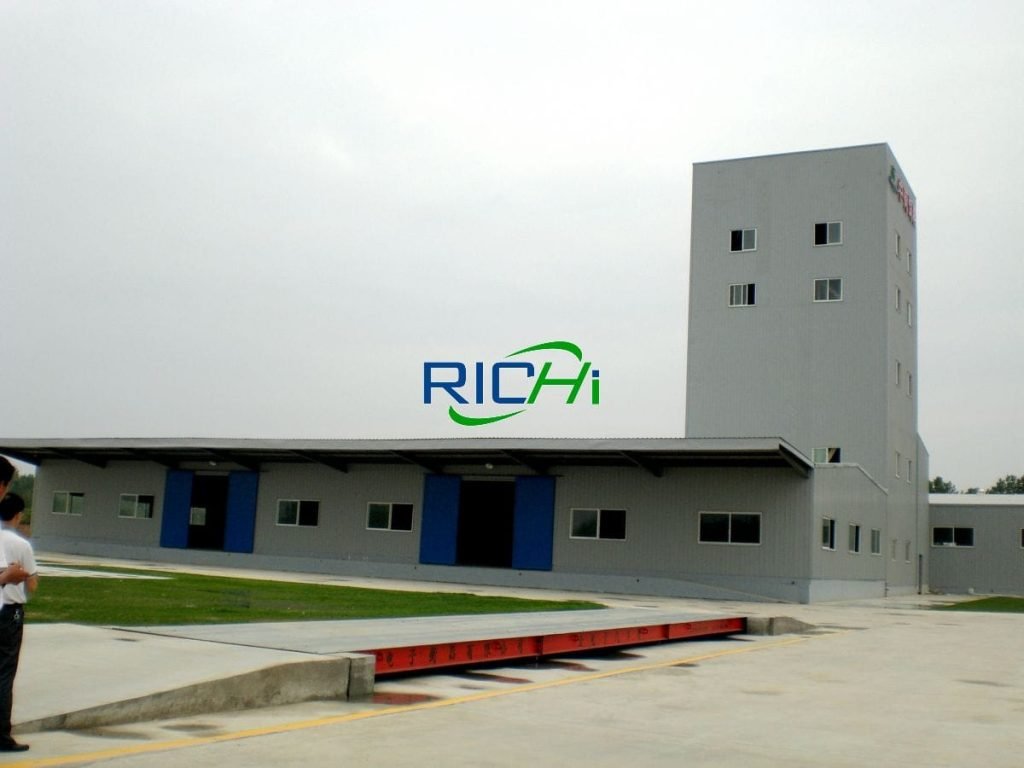
Related post: 4-5T/H Floating Fish Feed Plant
- The raw material receiving and cleaning equipment mainly includes weighbridges, primary cleaning screens and cylinder bins;
- Commonly used conveying equipment are screw conveyors, bucket elevators, scraper conveyors, belt conveyors and pneumatic conveying equipment;
- Pulverizing equipment includes magnetic separator, feeder, pulverizer, etc. Among them, there are many types of pulverizers, commonly used are hammer and claw pulverizers and micro pulverizers that require finer pulverization;
- The batching equipment generally adopts electronic automatic batching scales; the types of mixers used are horizontal double-shaft (single-shaft) paddle mixers, horizontal screw mixers, vertical mixers and waist drum mixers for the production of premixes;
- Granulation equipment includes steam boiler, conditioner, floating fish feed pellet mill, cooler, grading screen and crusher, etc.;
- Floating fish feed extruder machine includes conditioner and extruder; liquid spraying equipment includes liquid storage tank, vacuum pump and flow meter;
- Ventilation and dust removal equipment includes suction fans, brakes and dust collectors, etc.; packaging equipment includes packaging scales, sealing machines, etc.;
- The central control system is the “brain” of the entire floating fish feed making machine line processing process, where the control systems of various equipment are concentrated.
4. Quality control of floating fish feed making machine
(1)Equipment pre-design control
The technical staff will carry out scientific and reasonable design according to the actual conditions and requirements of the customer’s workshop, electricity, location, etc., combined with the floating fish feed making machine test situation.
(2)pare parts selection criteria
Spare parts suppliers, strictly screen the supplier’s products, and choose high-quality and low-cost manufacturers in the same industry. On the premise of ensuring quality, reduce floating fish feed making machine manufacturing costs and truly allow customers to purchase cost-effective equipment. For outsourced parts of the same variety, there are less than three suppliers guaranteed, so that the fittest can be purchased.
(3)Production control
After the sales department receives the order, it will be submitted to the technical department, and the technical department will produce the CAD drawings corresponding to the floating fish feed making machine according to the order details. The production department arranges a relevant part to purchase, produce and process according to the technical documents of CAD drawings.
(4)Equipment and spare parts acceptance
There are full-time quality control personnel to carry out batch inspection of outsourcing and outsourcing parts. Quality inspection is performed for key and precise spare parts. For self-made parts, self-inspection, mutual inspection and general inspection of processing personnel must be carried out, and all qualified parts can be put into use.
After the finished floating fish feed making machine is installed, it will be accepted by after-sales technicians. On-site equipment can be loaded for on-site debugging only after no-load operation for more than half an hour and no faults. Make sure that each equipment meets the floating fish feed mill factory conditions and issue the floating fish feed making machine certificate.