The installation process of a small feed making machine is a critical phase that sets the foundation for its efficient and reliable operation. However, if not carried out properly, it can lead to significant damage to the equipment, resulting in costly repairs, downtime, and reduced productivity. In this article, we will explore key strategies to prevent equipment damage during the installation of a small feed making machine.
1. Proper Site Preparation
Ensuring that the installation site is properly prepared is the first step in avoiding equipment damage. This includes:
- Leveling the Foundation: The foundation should be level and capable of supporting the weight of the machine and any associated equipment. Uneven or unstable foundations can cause misalignment and excessive vibrations, leading to premature wear and tear.
- Adequate Space: Provide sufficient space around the machine for easy access during installation, operation, and maintenance. Cramped spaces can make it difficult to maneuver components and increase the risk of damage.
- Electrical Supply: Ensure that the electrical supply at the site is adequate and meets the machine’s requirements. Improper electrical connections can lead to short circuits, equipment failure, and potential fire hazards.
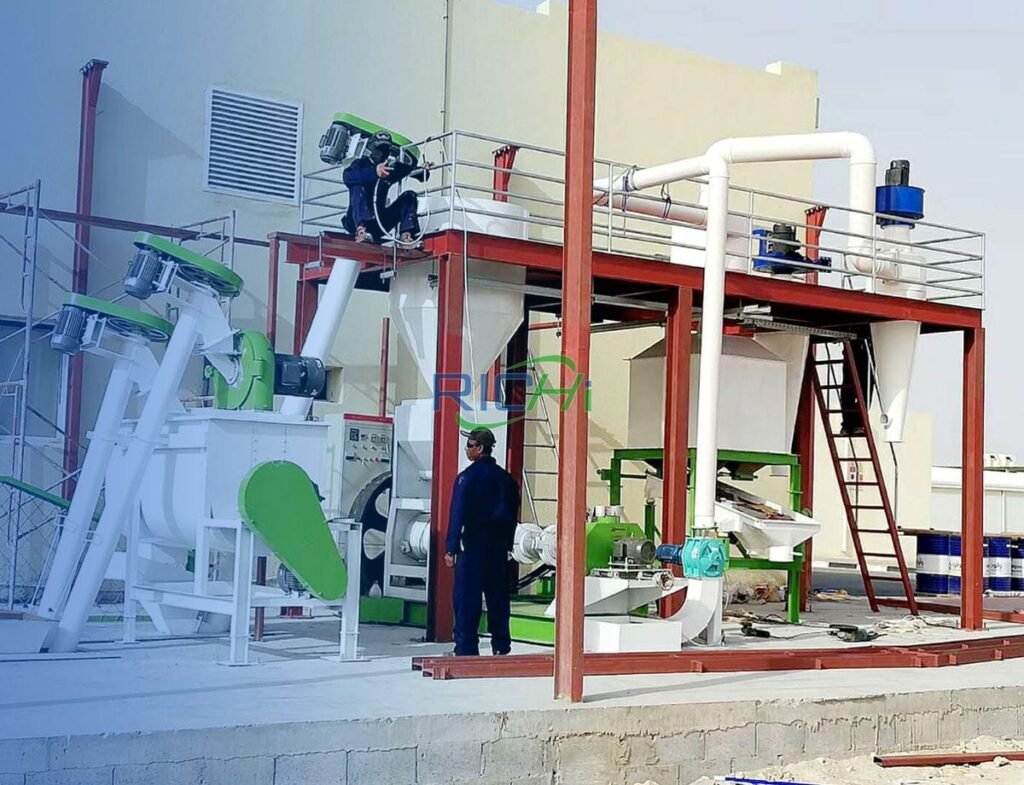
2. Careful Handling of Components
During the installation process, it is crucial to handle machine components with care to prevent damage. This includes:
- Proper Lifting: Use appropriate lifting equipment, such as cranes or forklifts, to move heavy components. Improper lifting techniques can cause components to fall or become misaligned, resulting in damage.
- Avoiding Impacts: Take care to avoid impacts or dropping components during handling. Even minor impacts can cause internal damage that may not be immediately visible but can lead to future problems.
- Protecting Surfaces: Cover or wrap components to protect their surfaces from scratches, dents, or other types of damage during transportation and installation.
3. Precise Alignment and Assembly
Precise alignment and assembly of the machine’s components are essential to prevent damage and ensure optimal performance. This includes:
- Shaft Alignment: Ensure that the shafts of the motor and other rotating components are properly aligned. Misalignment can cause excessive vibrations, leading to bearing failure and other mechanical issues.
- Proper Lubrication: Apply the correct type and amount of lubricant to all moving parts, as specified by the manufacturer. Inadequate or improper lubrication can cause excessive wear and tear, leading to equipment failure.
- Secure Fasteners: Tighten all fasteners, such as bolts and nuts, to the recommended torque values. Loose fasteners can cause components to become misaligned or come apart during operation, resulting in damage.
4. Comprehensive Testing and Commissioning
Before putting the machine into full operation, it is essential to conduct thorough testing and commissioning to identify and address any potential issues. This includes:
- No-Load Testing: Run the machine without any load to check for proper operation, unusual noises, or vibrations. This allows you to identify and address any issues before introducing raw materials.
- Load Testing: Gradually increase the load on the machine to its maximum capacity, monitoring its performance and making necessary adjustments. This helps ensure that the machine can handle its intended workload without causing damage.
- Calibration: Calibrate the machine’s sensors, controls, and safety systems to ensure they are functioning correctly. Improper calibration can lead to operational issues and potential damage.
5. Operator Training and Maintenance
Proper operator training and regular maintenance are crucial for preventing equipment damage and ensuring long-term reliability. This includes:
- Operator Training: Provide comprehensive training to operators on the proper operation and maintenance of the machine. Well-trained operators are less likely to make mistakes that can lead to equipment damage.
- Preventive Maintenance: Develop and adhere to a preventive maintenance schedule, as recommended by the manufacturer. This includes regular inspections, cleaning, and replacement of wear parts to prevent breakdowns and minimize the risk of damage.
- Spare Parts Management: Maintain an adequate inventory of spare parts to ensure that repairs can be carried out quickly and efficiently. Having the necessary parts on hand can help minimize downtime and prevent further damage to the machine.
Conclusion
Preventing equipment damage during the installation process of a small feed making machine requires a comprehensive approach that addresses site preparation, component handling, alignment and assembly, testing and commissioning, operator training, and maintenance. By following best practices and adhering to the manufacturer’s recommendations, feed producers can ensure that their machines are installed correctly and operate efficiently, minimizing the risk of costly repairs and downtime.
Investing in proper installation practices not only protects the animal feed plant machinery itself but also contributes to the overall success and profitability of the feed production operation. As the demand for high-quality animal feed continues to grow, prioritizing equipment protection will be essential for maintaining a competitive edge in the market.